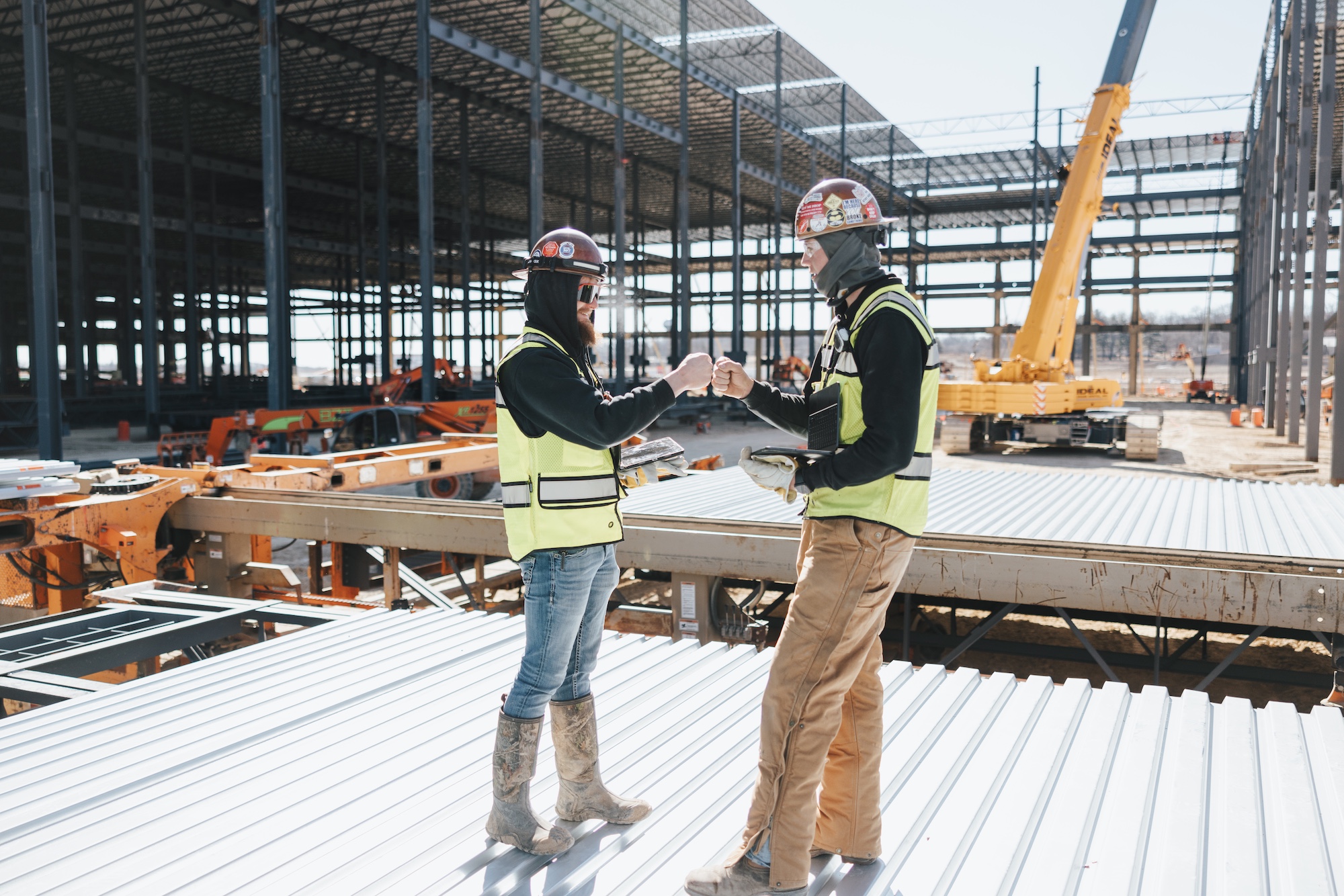
What Truly Binds a Team?
In reflecting, it’s not merely the deadlines we meet or the projects we complete—those are the surface ripples. The ‘benchmarks. In a strong team, you’ll find an unspoken p...
READ MOREDo you struggle with embracing training? Or integrating a Quality Management System? BZI had the same challenge.
Our Chief Training Officer, Justin Barlow recently presented at NASCC in Charlotte, North Carolina and emphasized that in order to successfully implement a QMS, there are key questions an organization needs to answer:
Answering the “who” question first is vital in understanding the “why” in a QMS. It’s important to understand the needs of the stakeholders. Involved parties in steel erection and fabrication include field team members, steel companies, general contractors, owners and jurisdictions, each with their own sets of needs, priorities, concerns, and motivations. Properly understanding the needs at every level of the stakeholder journey provides a path to providing necessary training and addressing questions at each level, leading to buy-in for the standards and the QMS system overall.
Through our time of developing a QMS, we’ve learned several lessons:
At BZI we’ve seen several benefits of QMS adoption, including:
QMS development and adoption certainly has not been an easy process for us, but it definitely has been worth it. By understanding the needs of different stakeholders, appointing an advocate, and focusing on the front-line team, a QMS can be developed that enhances quality of service, improves customer satisfaction, and increases your competitive advantage.
In reflecting, it’s not merely the deadlines we meet or the projects we complete—those are the surface ripples. The ‘benchmarks. In a strong team, you’ll find an unspoken p...
READ MOREProject Silver Eagle, a multi-level, e-commerce, warehouse, is set to wrap up at the end of April, with final details expected to be complete by June. No project is without its ...
READ MOREBZI and its leadership keep rolling in the accolades. Cedar City Chamber of Commerce recently announced James Barlow has been named CEO of the Year as part of its “Best of Cedar ...
READ MOREI would like to express my profound gratitude for the incredible BZI team and for the privilege of being a part of it. I am continually impressed by the teamwork and genuine concer...
READ MORE